

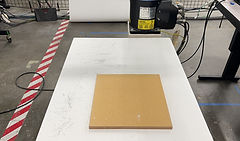






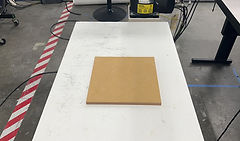

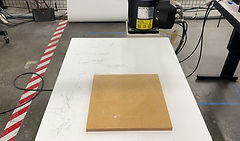


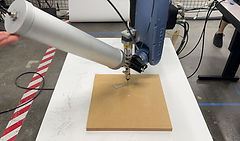

Robotic 3D Printing
Academic | UCLA | Technology Seminar | Winter 2022 - Spring 2022 |
Instructor: Curime Batliner | Shaun McCallum
Collaboration with: Kamila Khusnetdinova
This studio aimed at investigating the use of robotic 3D printing to develop fire resistant dwellings for fire prone regions of California. We are combining our research skills and our technical skills to understand the opportunities and limitations of robotic 3d printing. We are actively investigating both structural principles throughout the printing process but also the material science necessary when working with clay.
Where did it start?

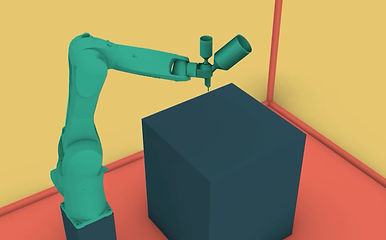



Form Evolution

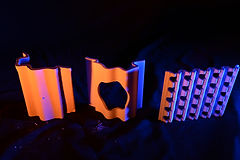


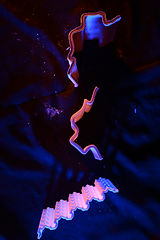
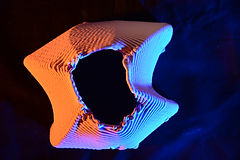

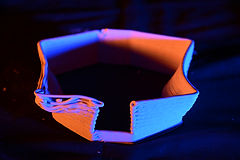

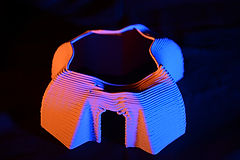


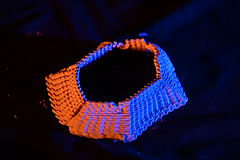



Toolpath Experimentation
Toolpath 01 - Linear
The linear toolpath uses the least amount of material & is the fastest to get printed but is very fragile to support the doubly curved surfaces of the structure.
Toolpath 02 - Weaved
The Weave is the most efficient toolpath for the structure. It uses more material & time as compared to the linear one but provides more support to each of the surfaces & strengthens the overall form.
Toolpath 03 - Deep Weaves
Since we got a successful strong print with the weaves we decided to try deeper weaves for the next one. And even though it used more material the strength was almost the same & overall the form was less cleaner.
Toolpath 04 - Waves
In this one we tried decreasing the density of the waves in order to use less material compared to the earlier two but obtain more strength. However, the strength in this one as well wasn’t as good as the second & 3rd one.
Toolpath 05 - Waves & Layers
Using the same density we tried staggering it through different layers but overall it wasn’t quite a successful print in terms of its strength & performance.
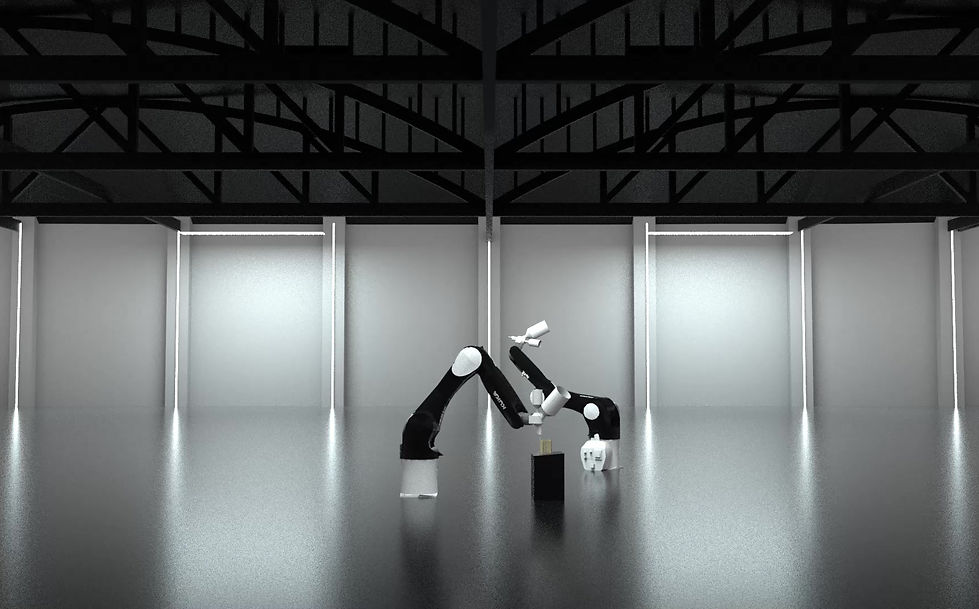